Struggling with Order Mistakes? How a WMS Can Improve Accuracy by 99%
Order fulfillment errors can result in lost sales, customer dissatisfaction, and wasted resources. A modern Warehouse Management System (WMS) can significantly improve accuracy, reducing errors by up to 99%.
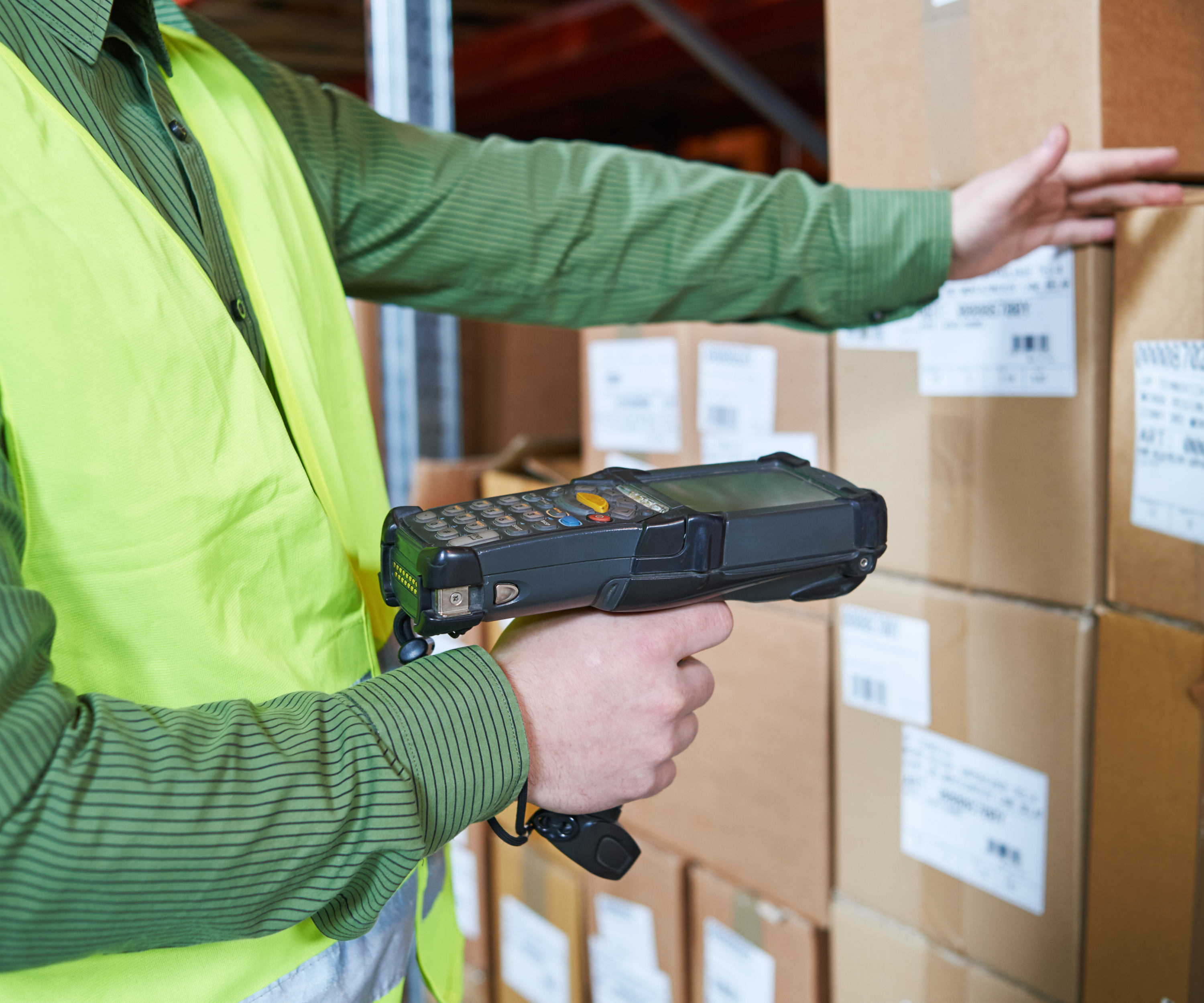
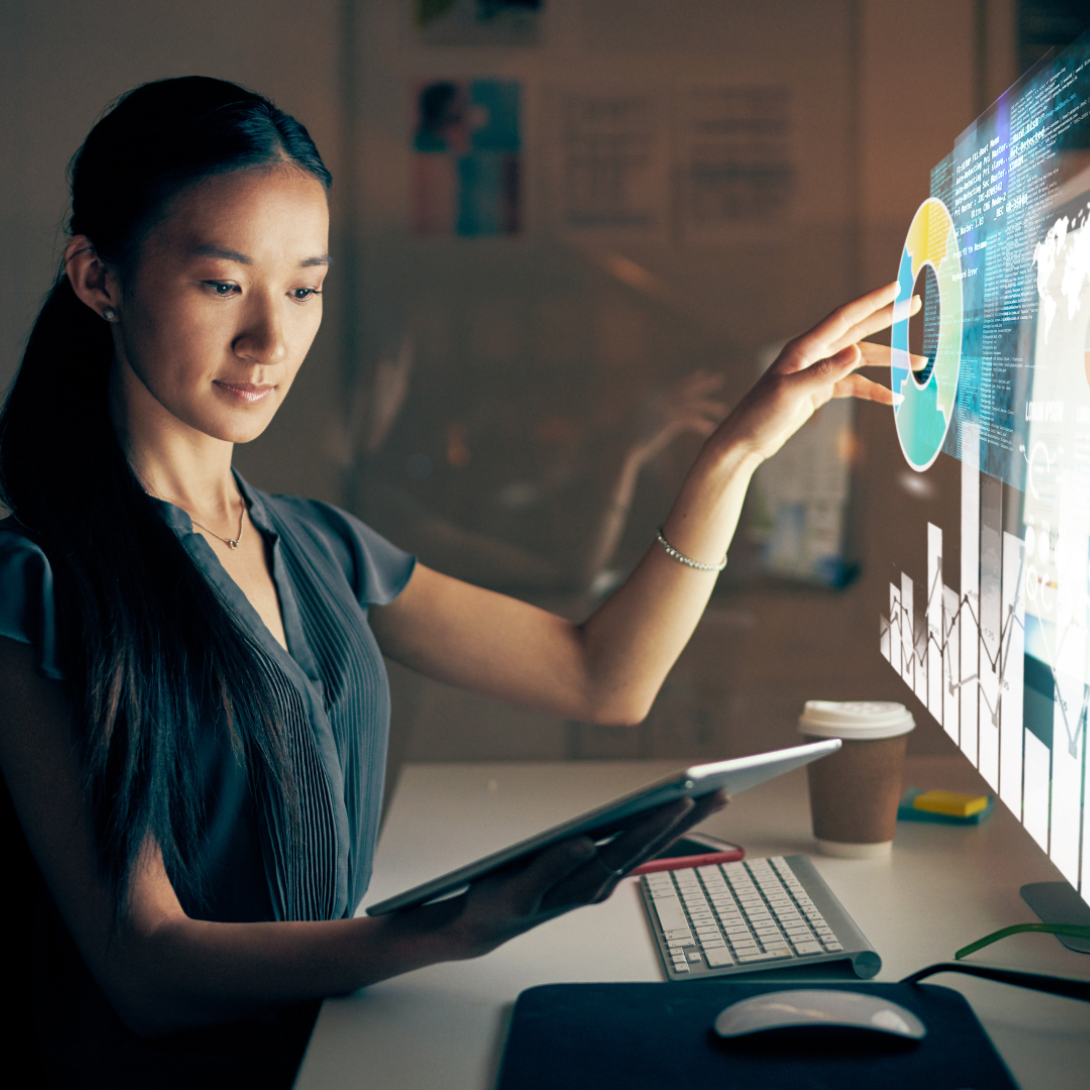
Struggling with Order Mistakes? How a WMS Can Improve Accuracy by 99%
Order fulfillment errors can result in lost sales, customer dissatisfaction, and wasted resources. A modern Warehouse Management System (WMS) can significantly improve accuracy, reducing errors by up to 99%.
Barcode Scanning
Using barcode scanning technology ensures that the correct items are picked for orders. As products are scanned throughout the warehouse, the system updates in real time, ensuring inventory accuracy.
Real-Time Inventory Tracking
A WMS provides real-time updates on inventory levels, allowing for more accurate stock management. This prevents overstocking or running out of stock, helping businesses avoid costly mistakes and backorders.
Automated Workflows
A WMS automates many manual processes, from order picking to packing and shipping. This reduces human error, ensuring that products are shipped correctly and on time.
Order Verification Systems
With built-in order verification steps, a WMS ensures each order is checked before it leaves the warehouse, reducing the chances of mistakes.
By implementing a WMS like Simpler WMS, businesses can eliminate errors and improve their order fulfillment accuracy.